Logistics and Supply Chain Management: How does it work?
April 11, 2019
Let’s suppose you need to print a document but ran out of paper for the copier machine, so you need to make a run to the store to buy a rim of paper. Ever wondered how that rim of paper land on the shelf of the store? Any retail store or company that sells a product most probably have a supply chain.
Today, we shine the spotlight on the industry of logistics and supply chain management. The terms logistics and supply chain management are blurry as it is commonly used interchangeably and is also debatable. For instance, what is known as supply chain management in the United States may be considered as logistics management in Europe. In Singapore, job seekers commonly look for positions by using the terms ‘supply chain’ or ‘logistics,’ or simply ‘jobs in supply chain.’
Today, we shine the spotlight on the industry of logistics and supply chain management. The terms logistics and supply chain management are blurry as it is commonly used interchangeably and is also debatable. For instance, what is known as supply chain management in the United States may be considered as logistics management in Europe. In Singapore, job seekers commonly look for positions by using the terms ‘supply chain’ or ‘logistics,’ or simply ‘jobs in supply chain.’
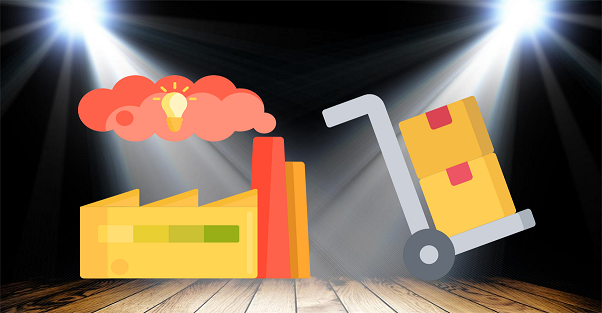
While the terms ‘logistics’ and ‘supply chain management’ may have their similarities or overlapping meanings, they are different in their concept. Supply chain management is the encompassing term that involves the process of a product from start to end. It links the different functions required to supply the goods in the chain process, whereas logistics has a specific objective, that is, to store, move and manage the flow of goods, and ultimately, to distribute and deliver the goods. Nevertheless, logistics and supply chain management intersect with each other in getting the job done.
Below is a visual example of what supply chain management looks like. The model may vary from company to company as each business has its own structure and organization.
Below is a visual example of what supply chain management looks like. The model may vary from company to company as each business has its own structure and organization.
First, on the left, we see product innovation and development, this function is where a lot of thought is put into the product, designing it, and planning the development of the product and the process in the supply chain to produce it. We move on to procurement where the initiation of forming the physical product happens. Here is where sourcing for raw materials and necessary equipment happens, followed by purchasing it. After purchasing, the raw material is stored as inventory at the warehouse. The manufacturing process begins by turning raw materials into a meaningful product. Depending on how complex the product is, the manufacturing process may take longer or shorter. Once the finished product is ready to go, the logistics team will store or send out the goods accordingly!
The customer service team is responsible for fulling the orders and coordinates between the different functions to fulfill the order, it is also their duty to track the order and update customers on the process. Other functions are also vital to supply chain management. The sales and marketing team will market, promote and sell the products, they are key people in managing the relationship with clients. The business development department strategizes on how to boost efficiency and increase productivity, with the goal to increase the success of the business. Finance, IT and HR departments also support the process just as they would in other businesses, such as managing manpower and their welfare, ensuring workers are paid and finances are healthy.
The customer service team is responsible for fulling the orders and coordinates between the different functions to fulfill the order, it is also their duty to track the order and update customers on the process. Other functions are also vital to supply chain management. The sales and marketing team will market, promote and sell the products, they are key people in managing the relationship with clients. The business development department strategizes on how to boost efficiency and increase productivity, with the goal to increase the success of the business. Finance, IT and HR departments also support the process just as they would in other businesses, such as managing manpower and their welfare, ensuring workers are paid and finances are healthy.
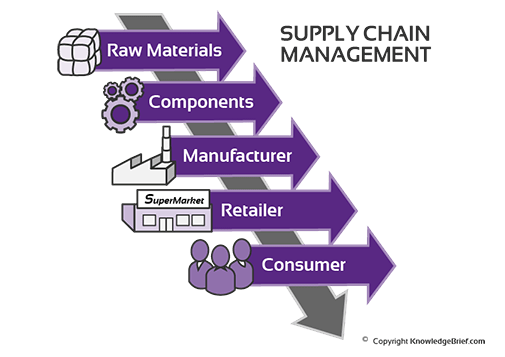
Taking paper as an example, wood pulp and plant fibers from logs are needed to form paper. Logs are the main raw materials sourced for and purchased. Especially since we are all making efforts to go greener (or really just to reduce costs), other materials could include recycled newspaper and cloth. Automated machines such as grinders, revolving slabs, and fourdriniers are also necessary to process the raw materials by altering their form. All these components are gathered together, and the manufacturing process begins. In making the pulp, logs are thrown into drums, grinders, digesters, and cooked into a chemical solution until the broken-down chips turn into pulp. It moves on to the next stage called beating. The pulp is put through a process of pounding, squeezing and beating. Paper comes out as the finishing product according to specifications such as size, texture, and design. The finishing product passes through the packing stage and the logistics team arranges and schedules for delivery to warehouses, wholesalers and retailers. And, that is how the rim of paper we need for our copier machine land on the shelf of retail stores for us to grab, purchase, and use!
Knowing the context of the industry we work in will give us a sense of where we stand and how we are contributing to the company. Whether it is our current work or potential job, the knowledge of the bigger picture of our work will improve the way we work when we know why we are doing what we are doing – we know the purpose and the end goal!
Knowing the context of the industry we work in will give us a sense of where we stand and how we are contributing to the company. Whether it is our current work or potential job, the knowledge of the bigger picture of our work will improve the way we work when we know why we are doing what we are doing – we know the purpose and the end goal!
Topic(s): World News and Insights
Singapore’s Work Holiday Pass and Training Employment Pass
Power of LinkedIn for Your Career